Roger Krulak, CEO of FullStack Modular describes a paradigm shift in construction that is revolutionizing multifamily development. Krulak dives into the benefits of modular construction and the overall impact it is having on the CRE industry.
VIEW PRESENTATION:
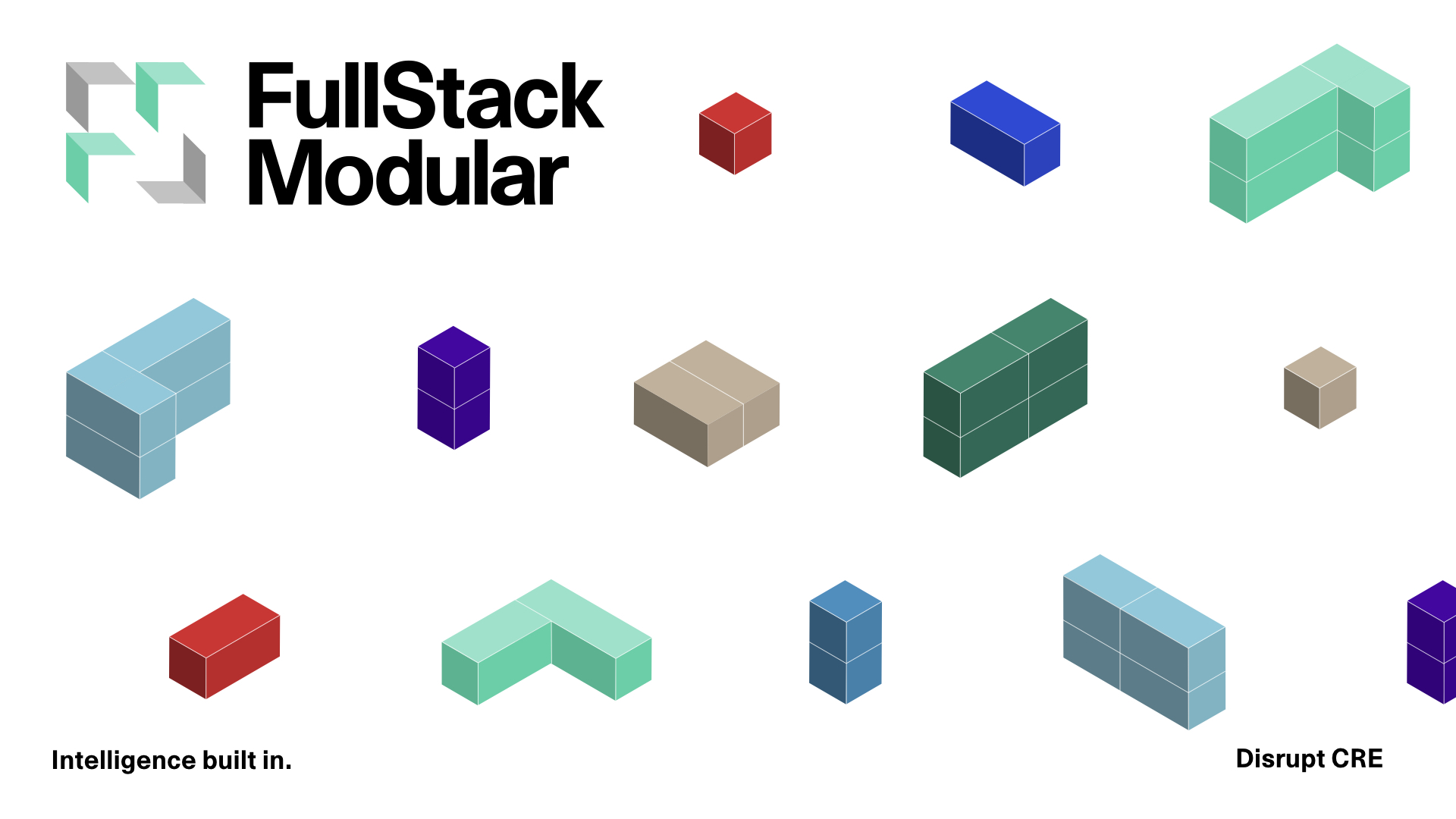
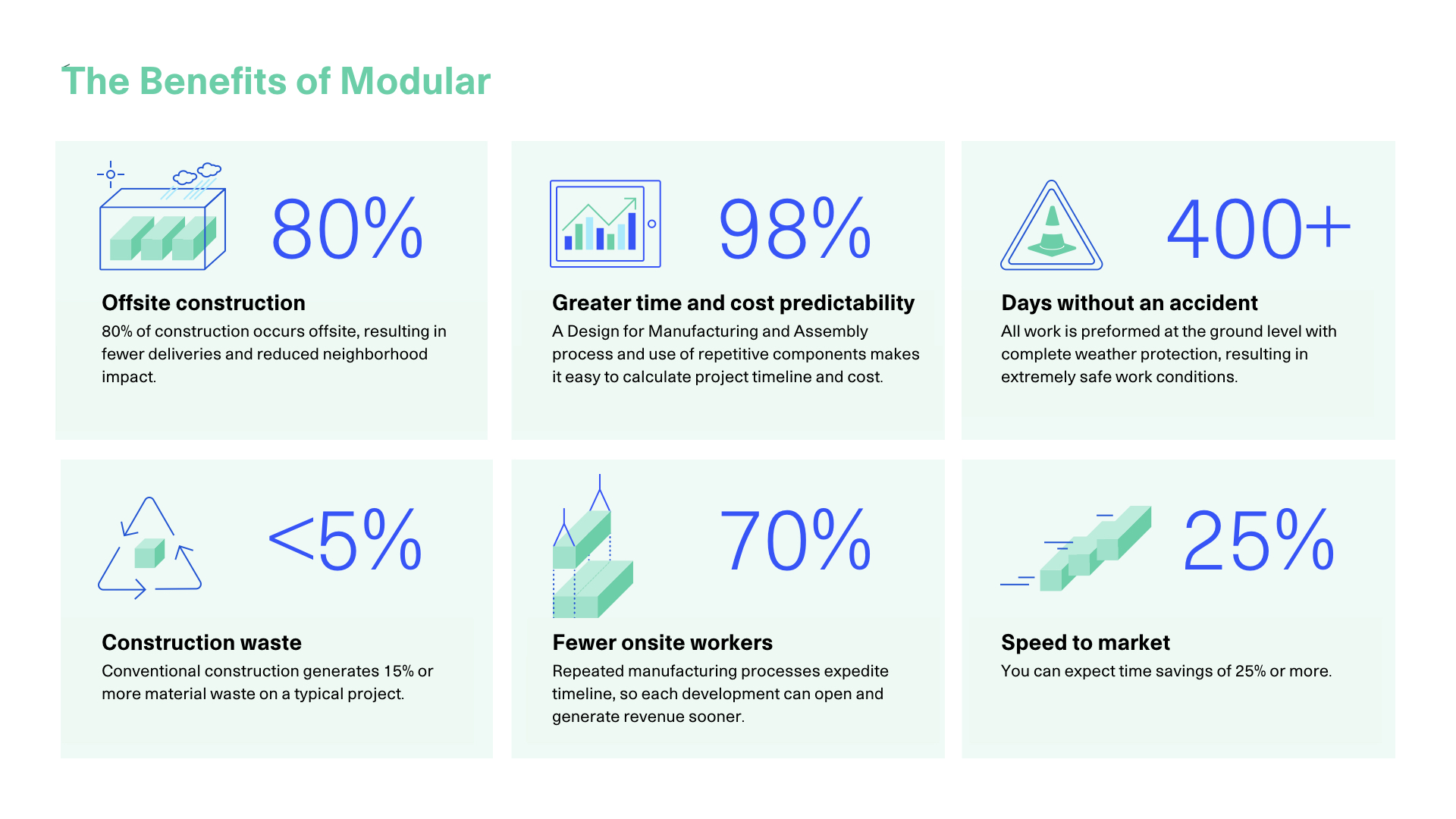
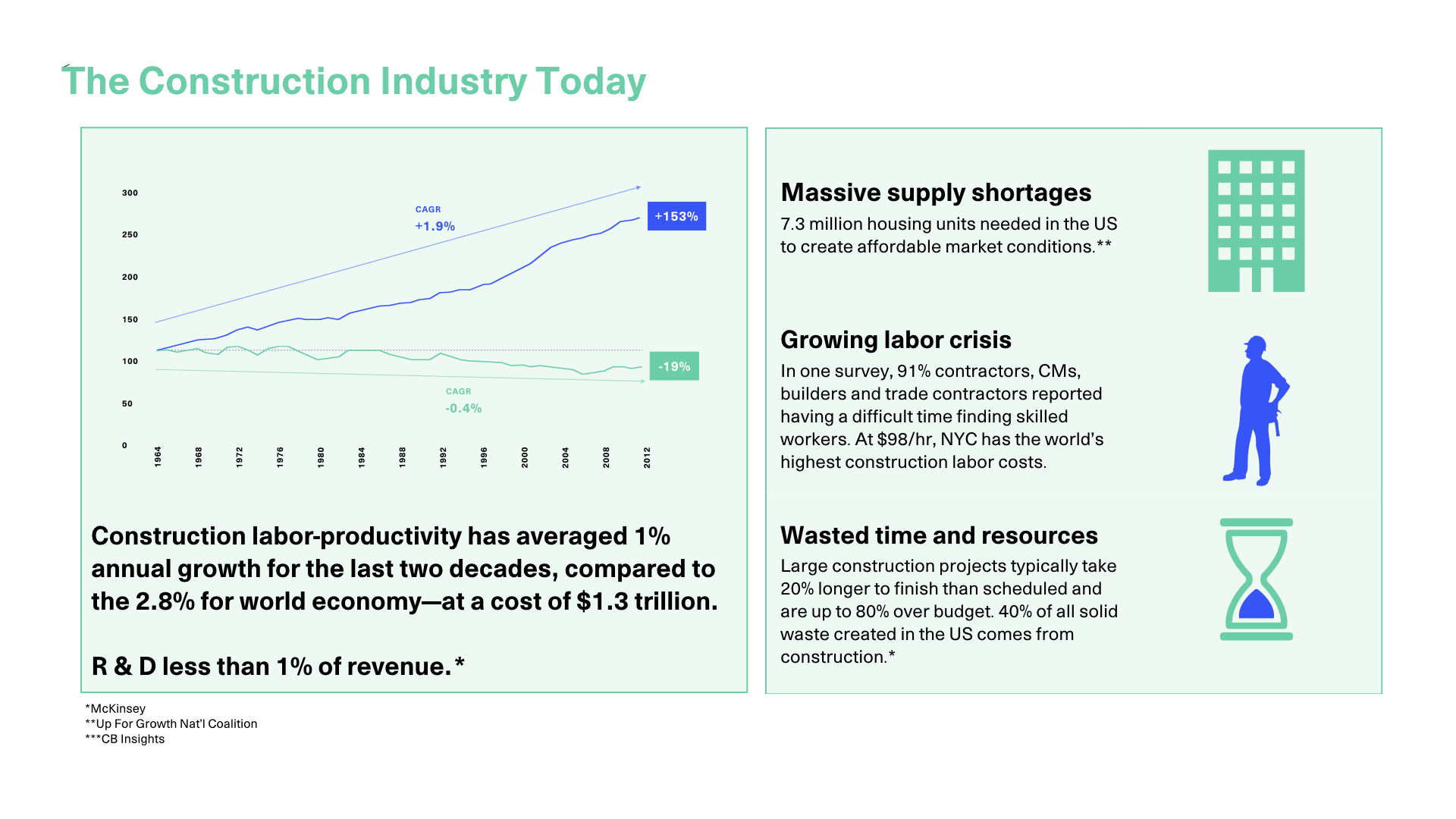
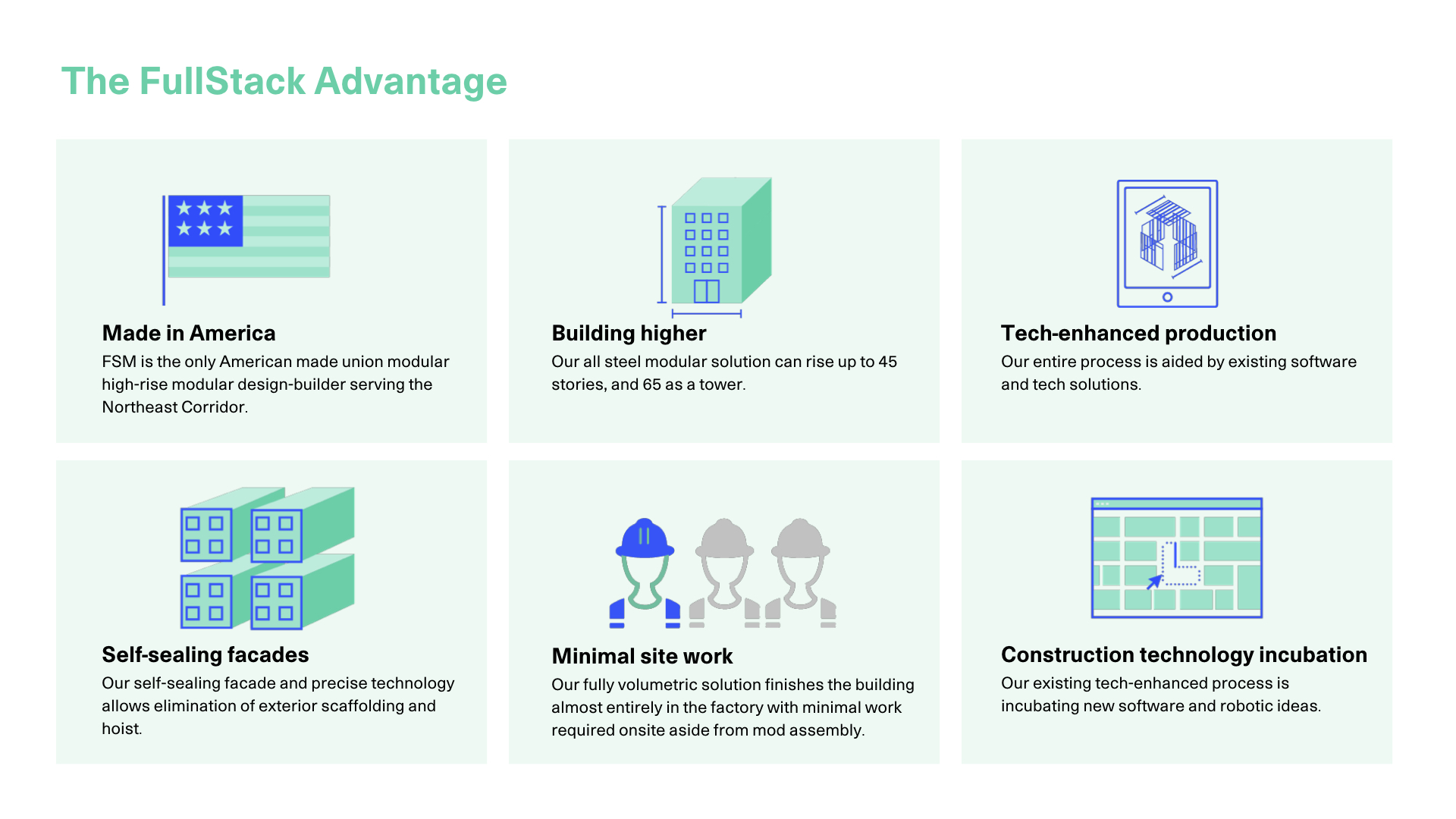
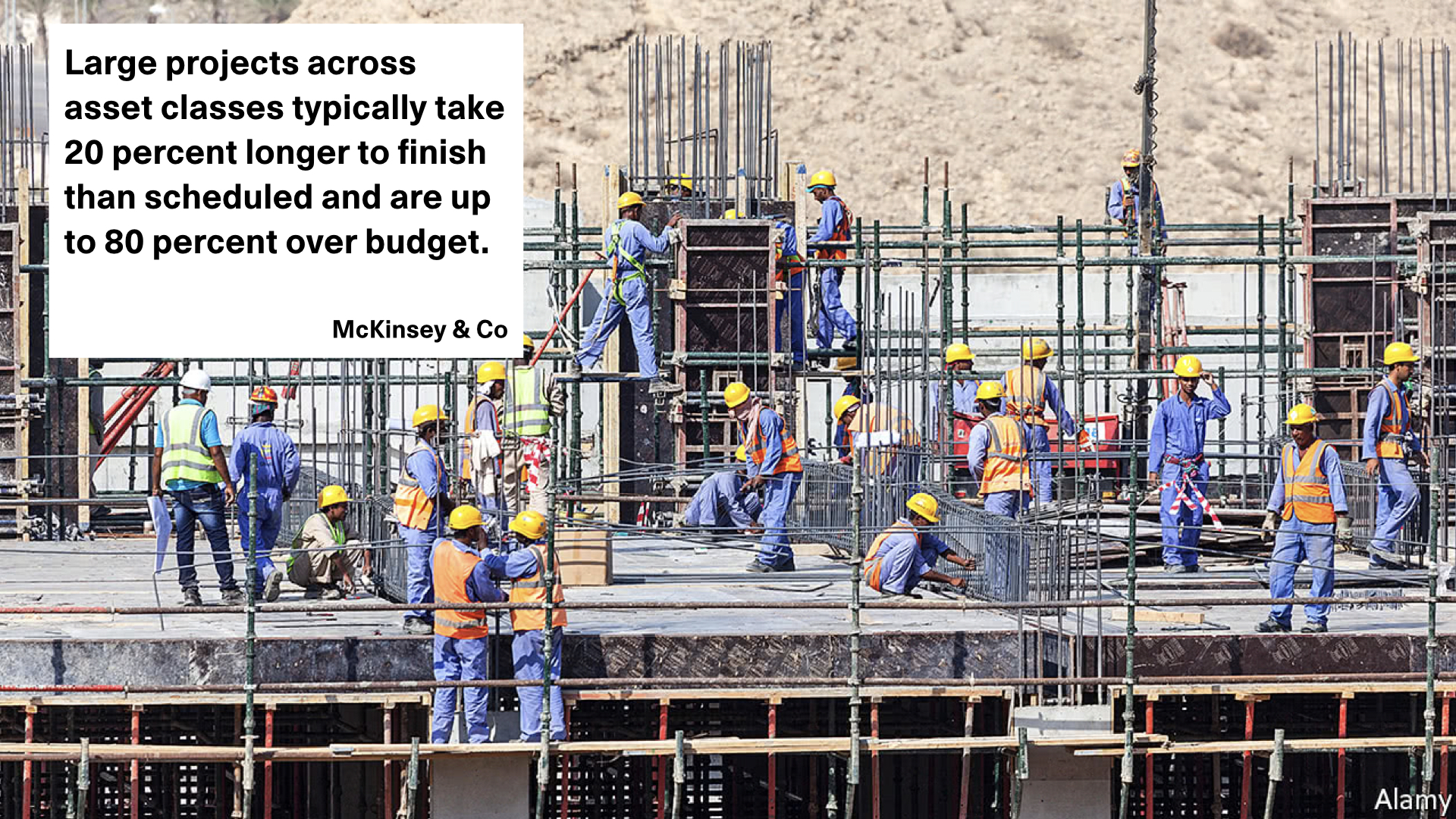
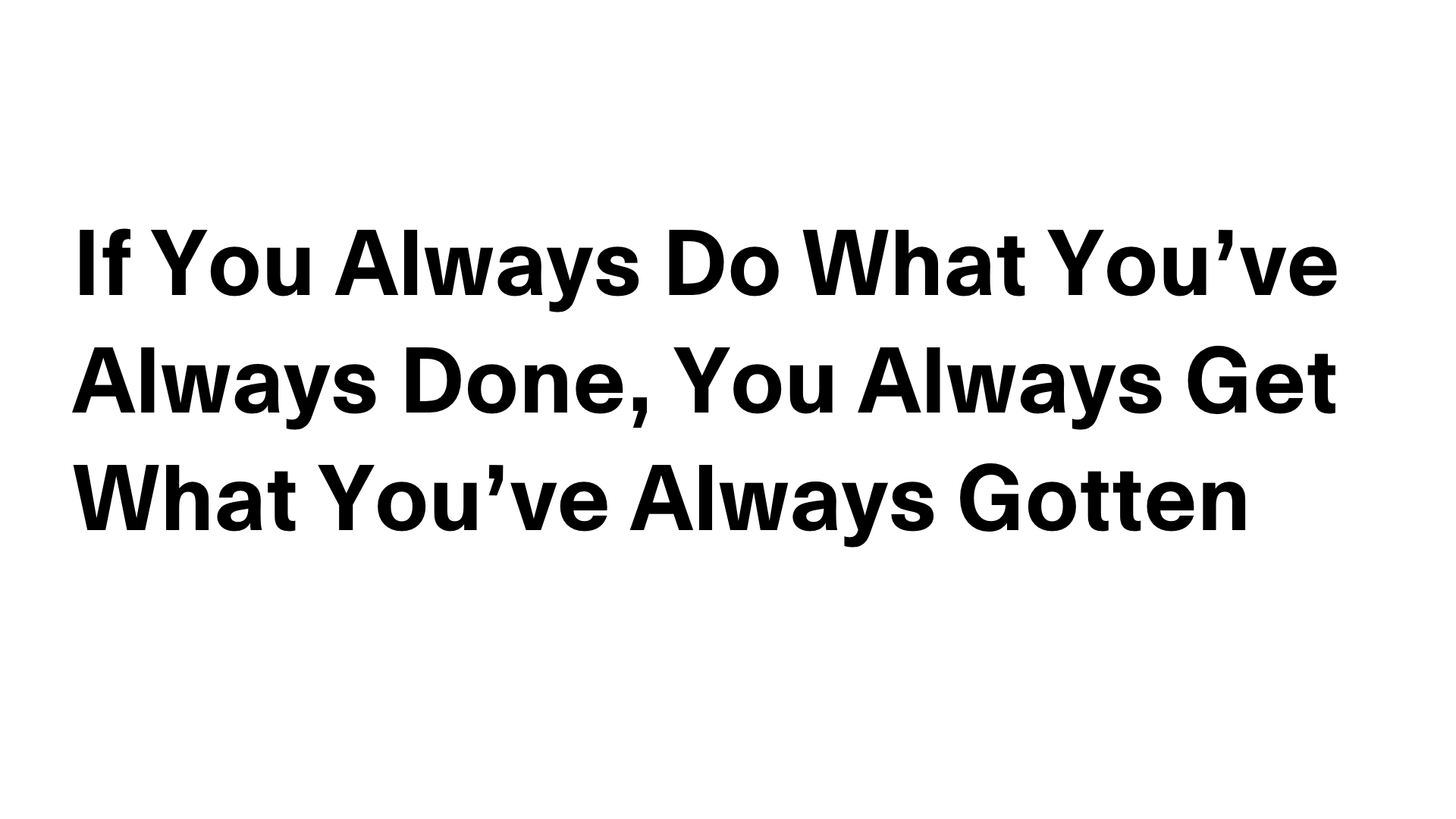
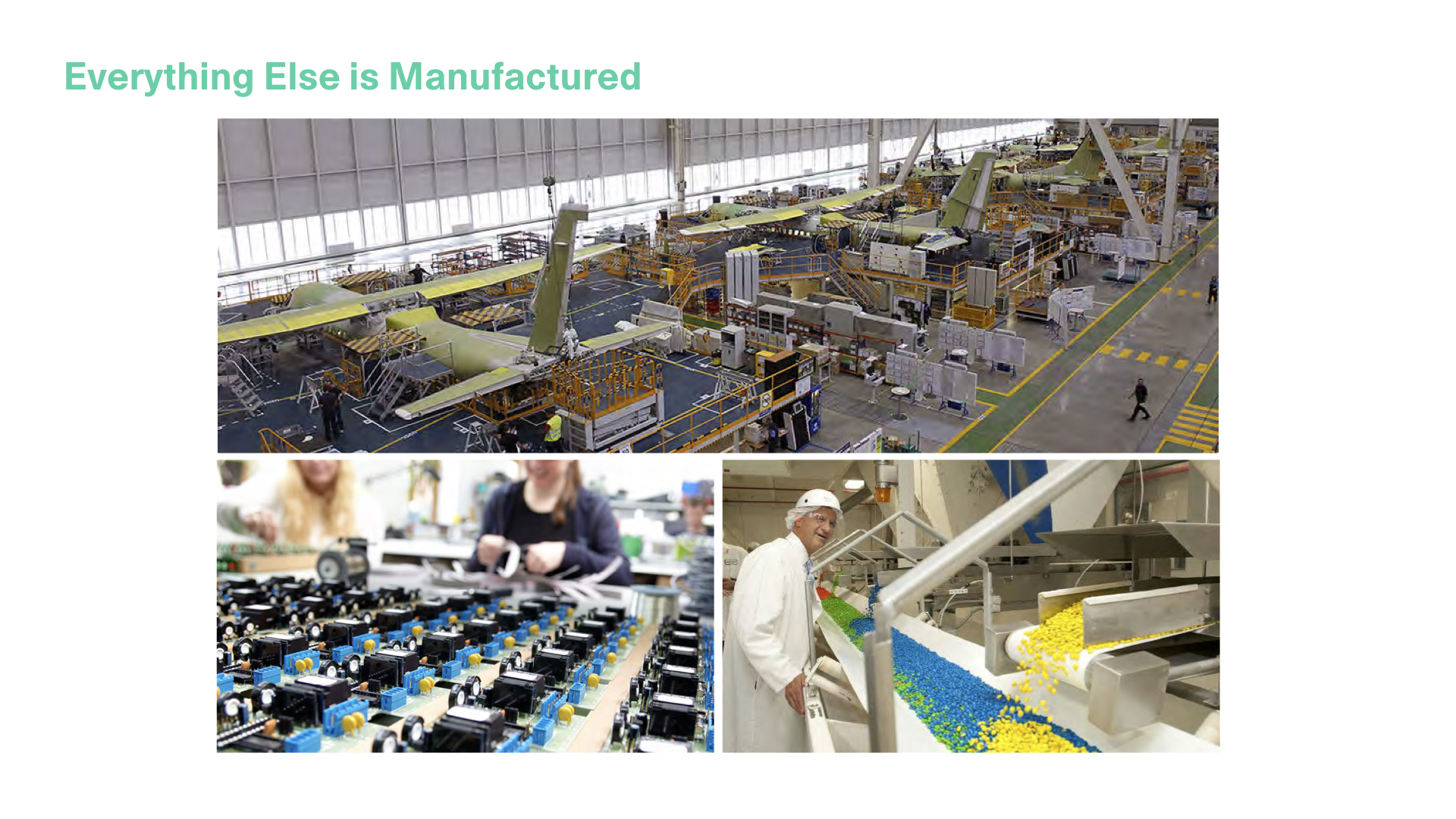
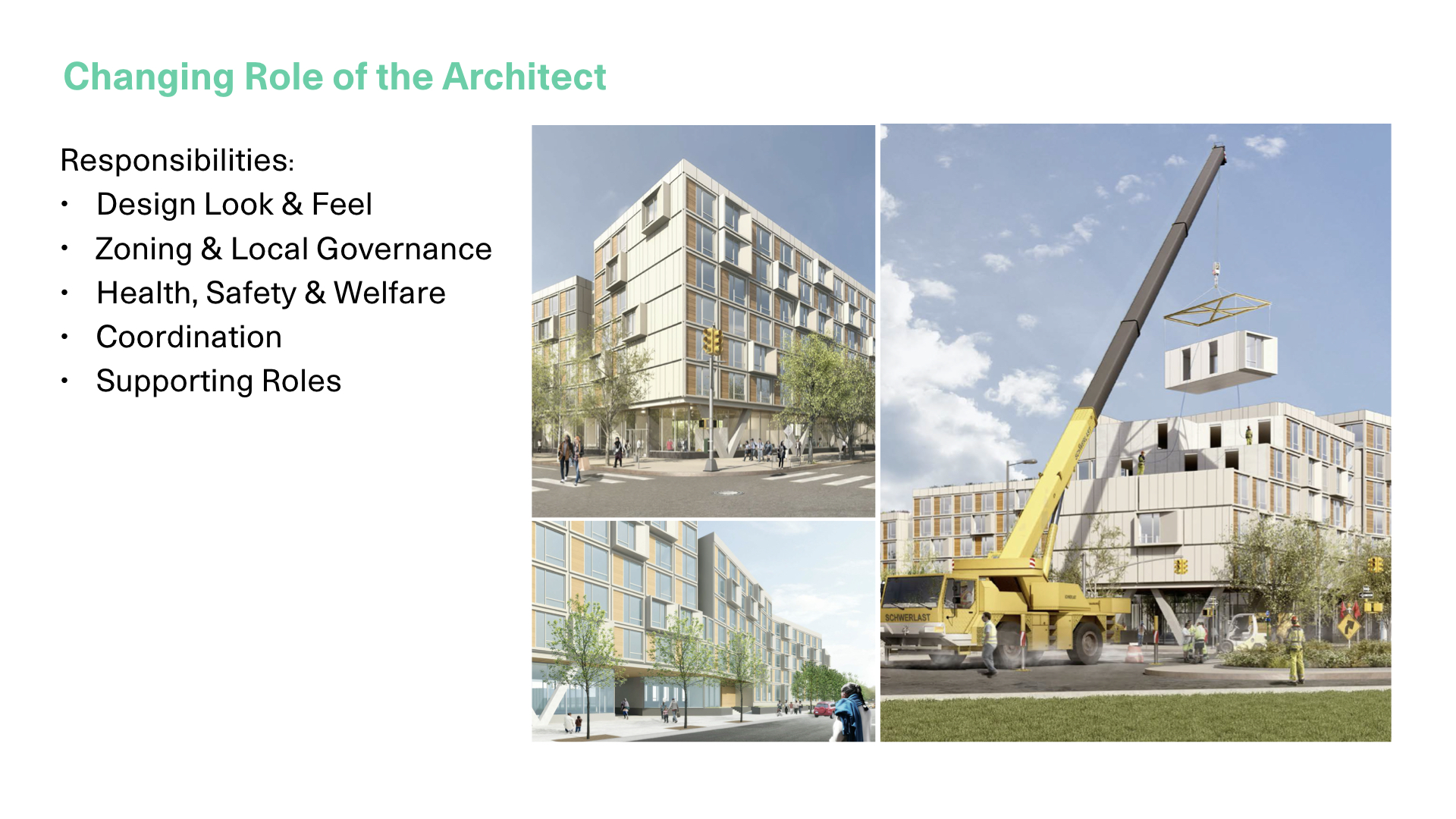
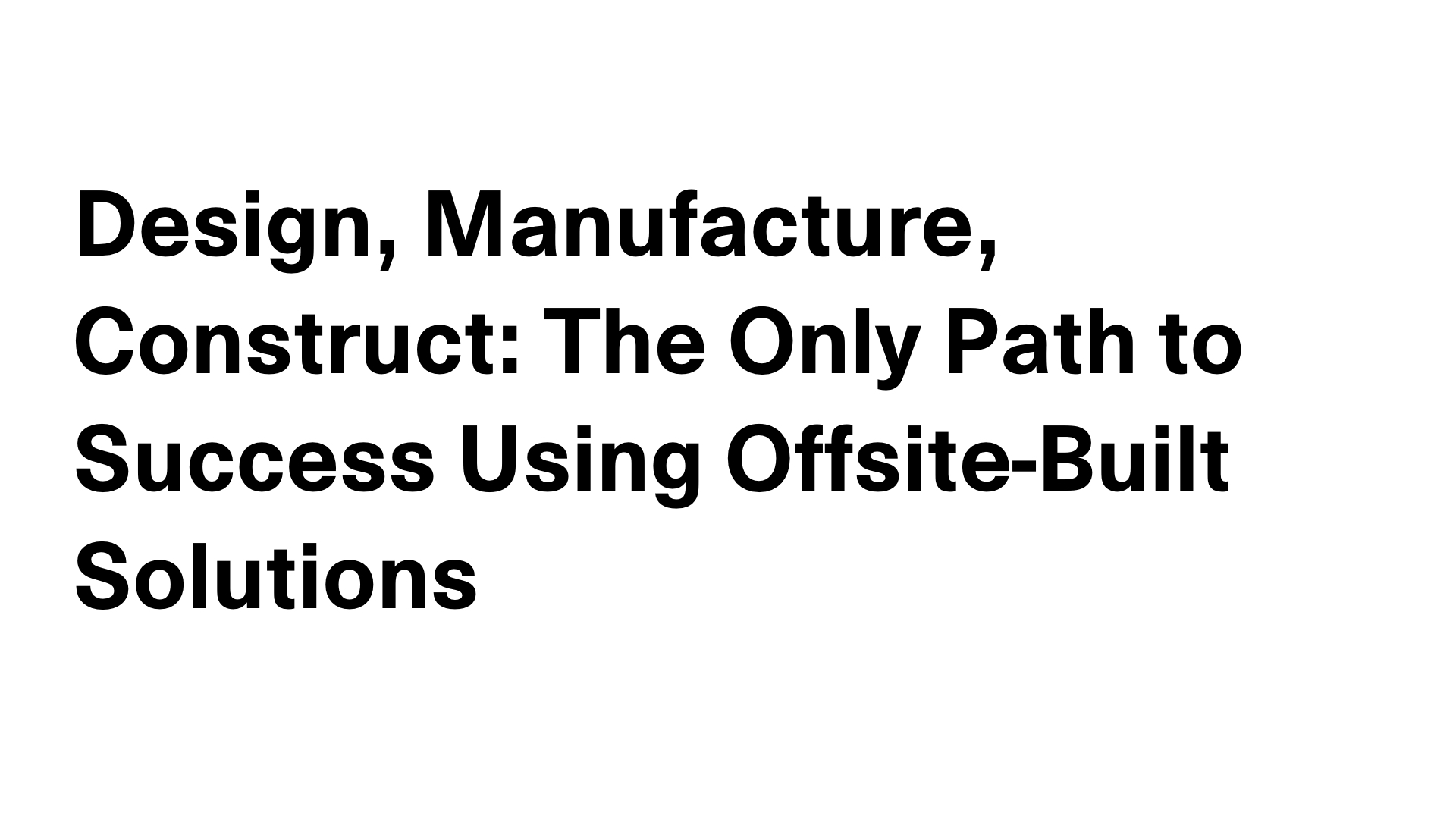
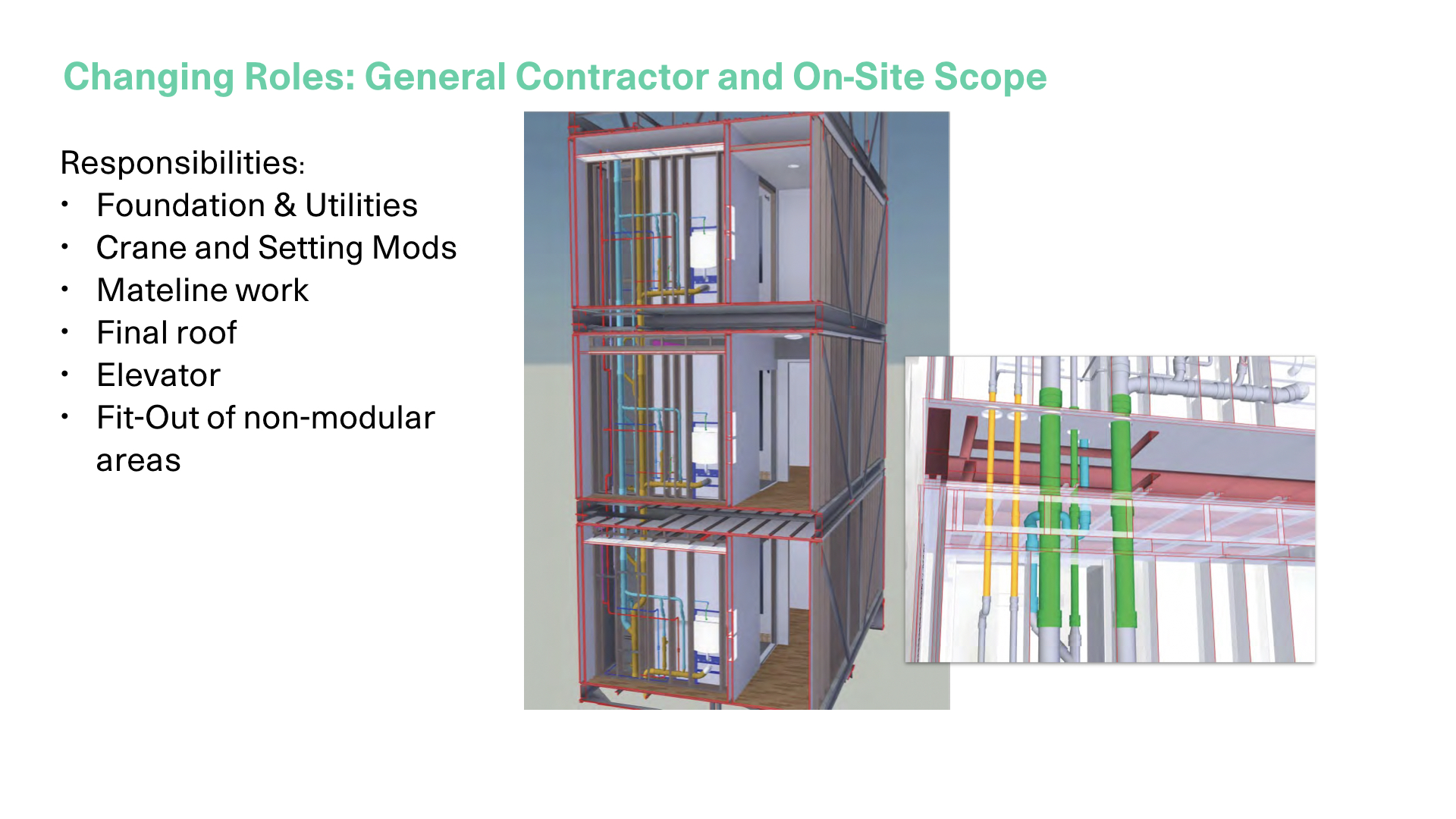
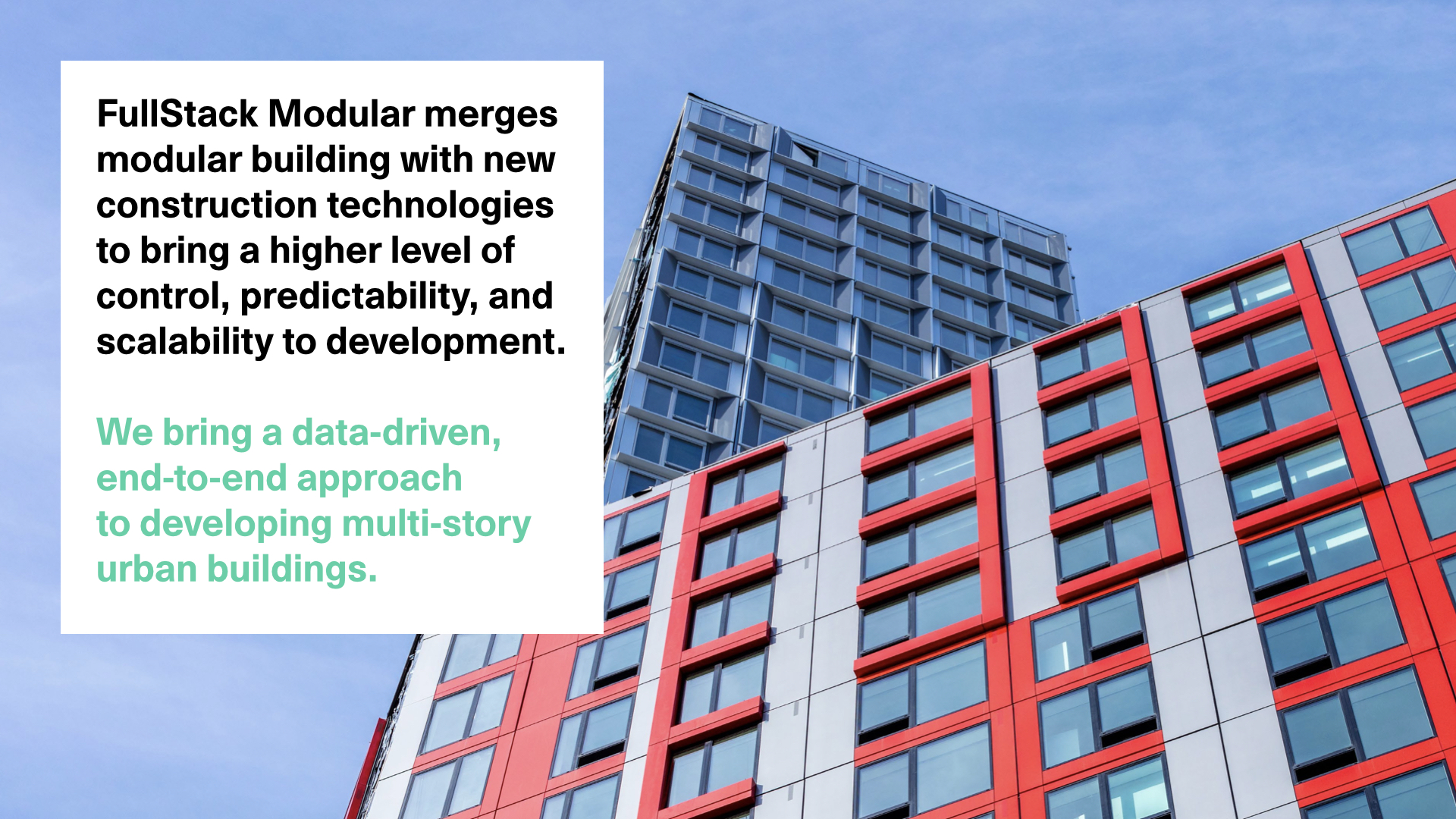
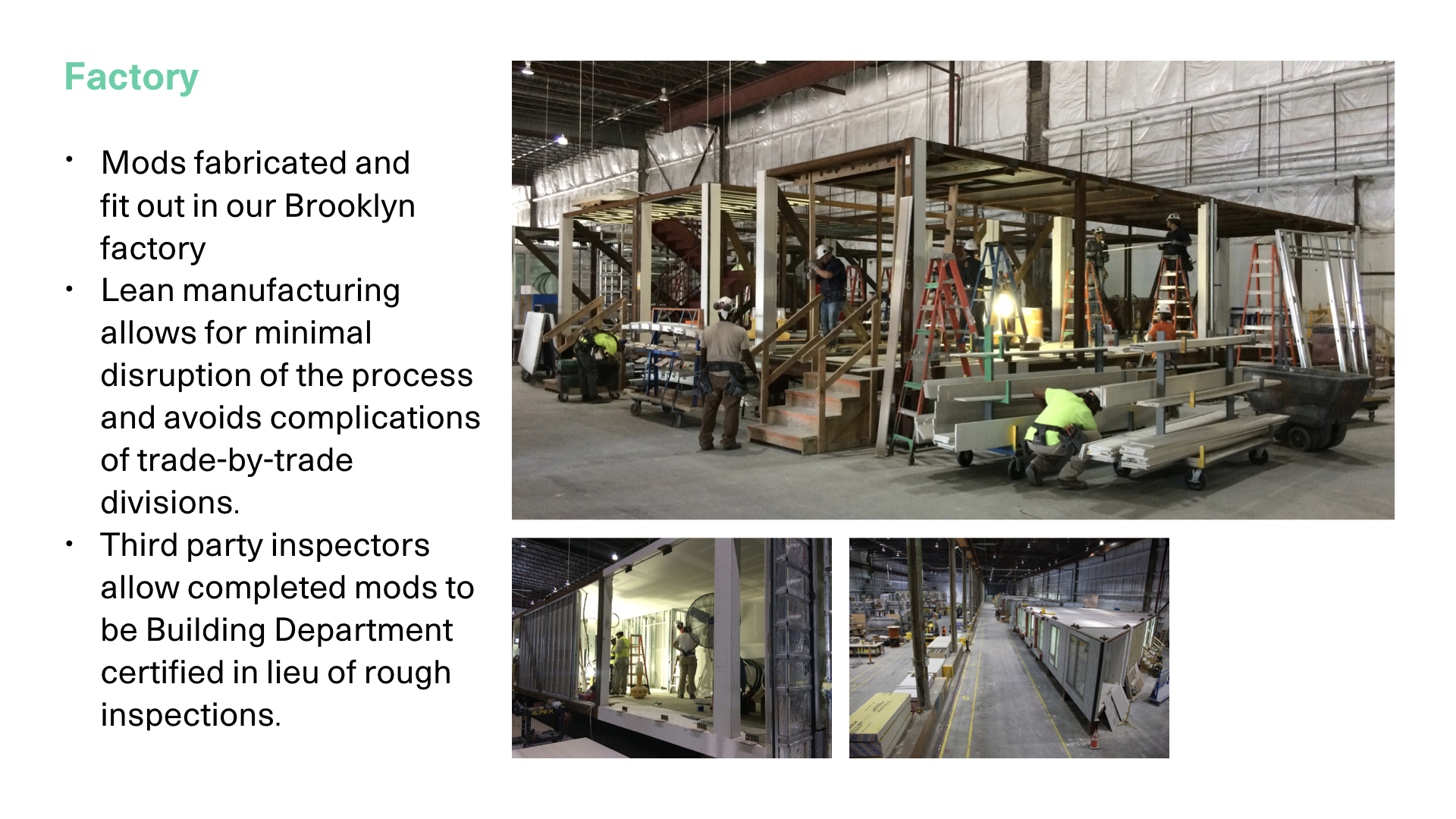
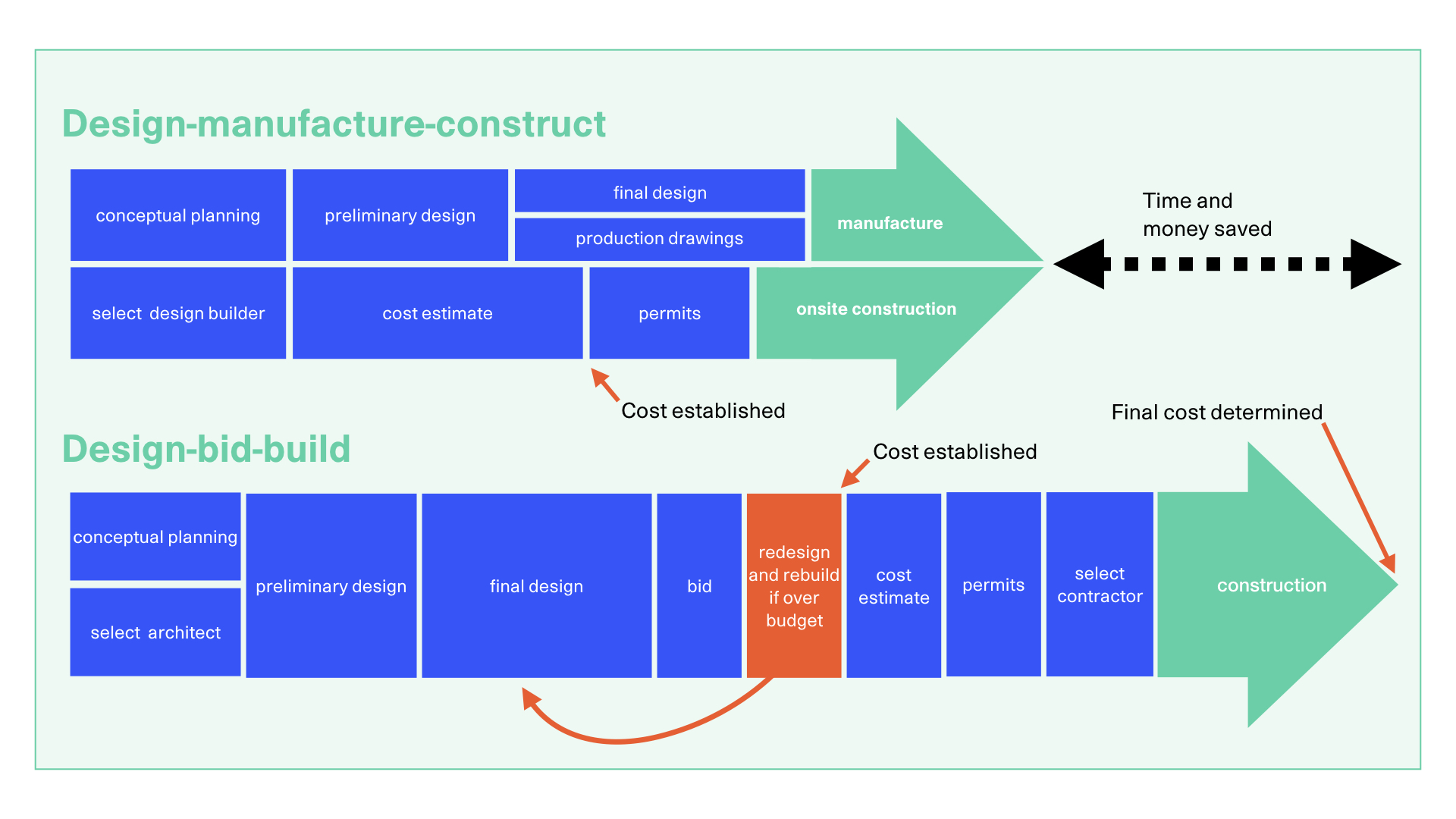
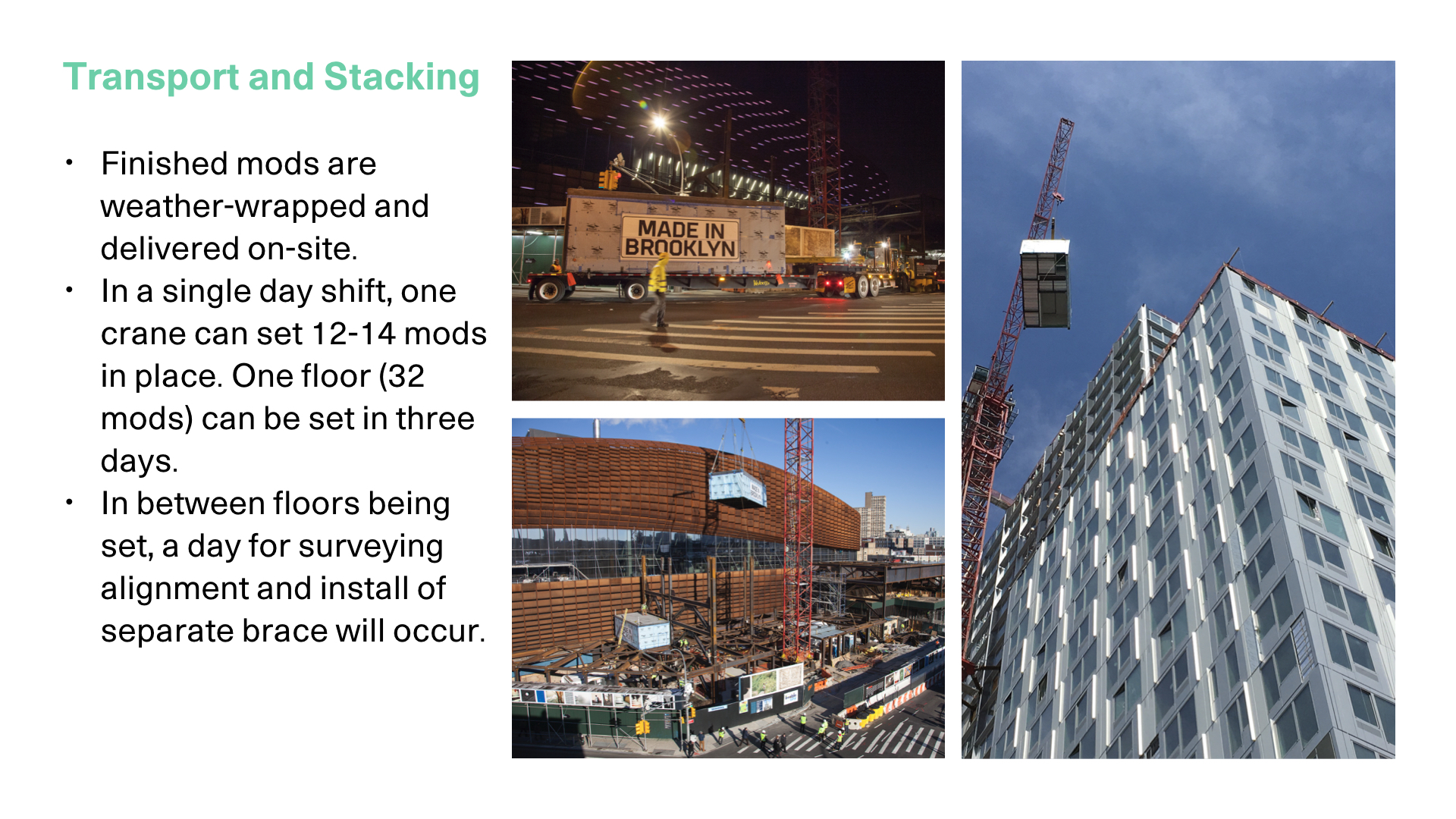
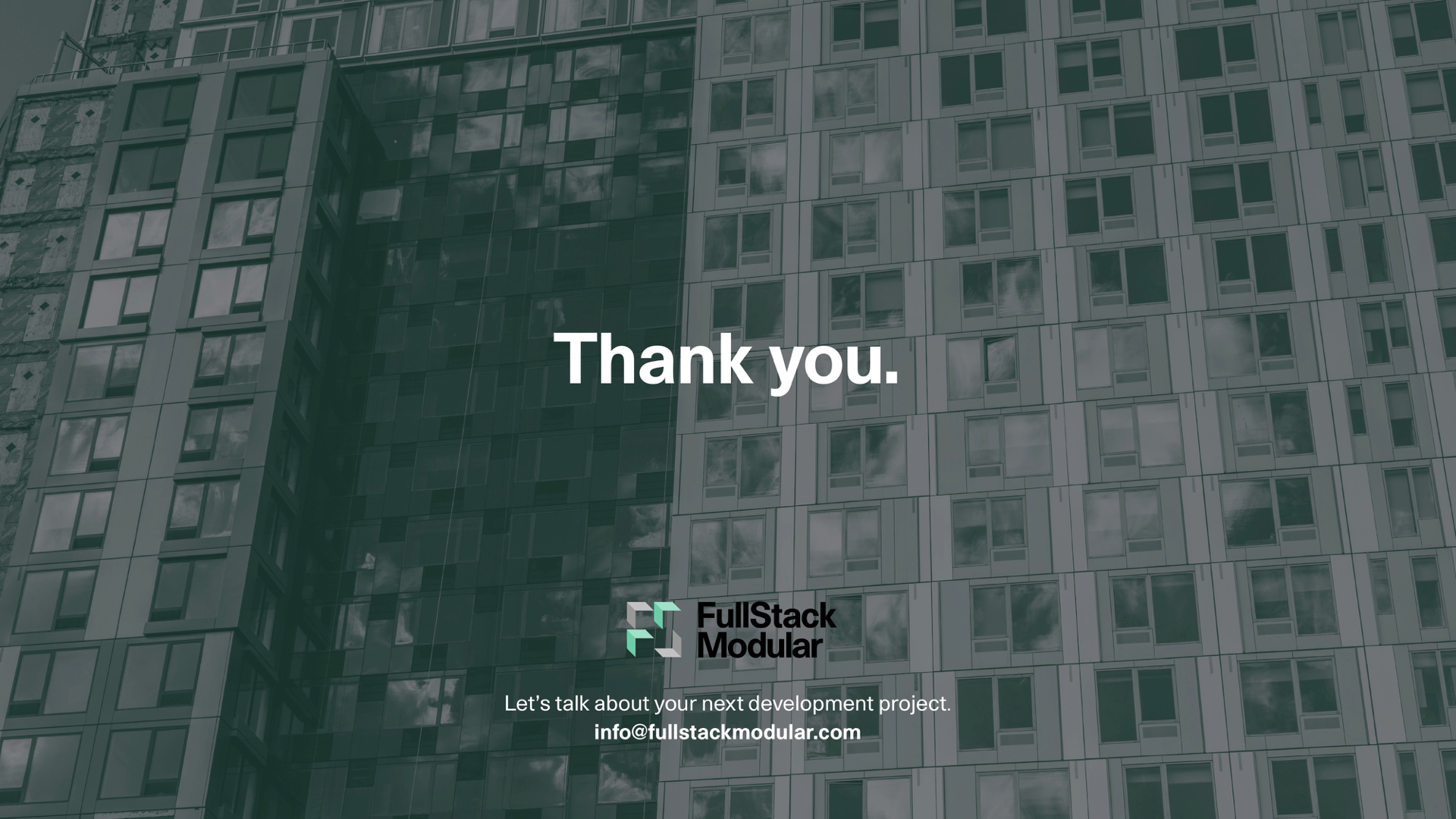
VIDEO TRANSCRIPT:
Hello I'm Roger Krulak. I'm the CEO and founder of full stack modular we are a fully volumetric solution for high rise multifamily buildings in a dense urban environment. So today I'm here to talk about the crisis of lack of productivity in the construction industry. There are three major drivers, one of them is that we are not meeting the current needs for housing for instance in the United States. There is at least a 10 million housing unit deficit as we speak today. In addition to that there is an increasing lack of labor for productivity for the built environment, less people are going into the trades or the boce trades in this country.
Additionally the process of construction in the United States and frankly in the world is broken. Projects normally end up at least 20 percent over schedule budget and as much as 80 percent over construction budget. This is part of the reason why the productivity on site is completely disorganized the process of organizing construction by trades is nonsensical from a logical process perspective.
Everything else in the world is manufactured. Aerospace, airplanes, toys candy is manufactured but construction is not. Designed manufacturer construct which is what we do at full stack is the only path to success using offsite built solutions or using manufacturing to construct the built environment. Full stack modular utilizes technology and manufacturing processes to increase the efficiency by which we create the built environment.
Here you see an example of the traditional method of construction which is design bid build against design manufacturer construct solutions and you can see not only is there an opportunity to save time which is of course a major goal but you also can decrease the amount of time that it takes to get the cost efficiency. And that happens by creating a digital twin of the building before we ever build it costing it out and organizing it in a process that is as efficient as possible.
In addition to allowing you to build the foundations etc on site while we're actually manufacturing in the factory increasing both productivity, predictability and cost. Some of the benefits of modular construction and in our solution is that we build 80 percent of the building off site. It's 98 percent cost predictable, we only calculate in the factory labor material and overhead rather than organizing it by trades.
It's incredibly safe. Employees almost never get above 30 inches off of the floor. We have almost no waste. We have less than 70 percent of the workers on site making it a much safer solution and at a minimum you're gonna get a 25 percent increase in time to market. Additionally a full stack modular has some other advantages. We are made right here in the United States. We can build incredibly tall buildings with our solution forty five stories and a double loaded corridor and up to sixty five stories in a tower configuration.
We implement technology within our process. We have a cell ceiling facade solution. We have almost no or few workers on site. Once the once the modules leave the factory and get installed on site and we are always incubating new technologies in order to increase that efficiency. It’s a value proposition for manufacturing in lieu of conventional construction. So if you always do what you've always done you always get what we've always gotten. So the problem is why isn't everybody doing this.
The reason everybody isn’t doing it is that it requires a significant paradigm shift in the process that we create the built environment and the roles change significantly. For instance the architect normally is involved at the very beginning of thinking about how the building is going to be built and then what it might look like and what the program is and we're trying to shift the role to architecture whereby they worry about the way that the building looks and reacts to the environment and the way that the people in it react to the building.
We take care of all of the math of the massing of the processing. Technologically. And the role of the general contractor significantly changes and these are some of the ways they are the scope of work that happens. It starts with foundation and utilities which is generally conventional the crane in the stack of the models we bring the models from the factory they get stacked in about 12 minutes we do mateline work and the mateline work and you may not know what that is, there's a picture here describing it.
There's three modules, they're stacked on top of each other. the mateline work is all the connection pieces that are required that happen on site whereas all of that mod work, all the distribution mechanical electrical plumbing happens in our factory. This is a picture of our factory. You can see how the modules are manufactured, assembled as we call it. You can fit up to fifteen thousand square feet of a building in the factory at a time. We manufacture between 5 - 7,000 square feet of finished product a week which includes elevators, stairwells, all of the structure all of the facades toilet paper holders paint lighting fixtures everything except for the hallway.
Once our modules arrive onsite either by truck or by train or by water it takes roughly 12 minutes to stack. The advantage of that is that the building is almost completely finished including stairwells, elevator shafts, all of the finishes in the units including and down to the toilet paper holder, painting, flooring, appliances, anything short of people. And there's no scaffolding required.
There is no hoist required and the building gets stacked up just like it's going to be finished. Thank you very much. Roger Krulak CEO and founder of full stack modular. Thanks for listening today.